BETHLEHEM TWP., Pa. — OraSure Technologies, which developed and now manufacturers tests for COVID-19, indicated Monday that a new Lehigh Valley location signals its commitment to meeting the pandemic head-on as well as the strength of American-made diagnostic products.
“I am very proud to share the results here behind us – that we have built the capacity and partnership to manufacture almost 2 million tests per week,” OraSure President Carrie Eglinton Manner said at a morning ribbon-cutting ceremony attended by U.S. Sen. Bob Casey, U.S. Rep. Susan Wild and other officials.
“And we will continue ramping up this capacity and ramp production into 2023.”
- Orasure Technologies held a ribbon-cutting ceremony for a new Bethlehem Township facility that will have 139,000 square feet of medical device manufacturing space
- The company attributed its success to three federal government contracts totaling more than $337 million it was awarded last year
- The facility features warehouse space for bringing in raw materials, a staging area, formulation suites and production cells with automated assembly lines and machinery
OraSure Technologies is a developer and manufacturer of point-of-care diagnostic tests and specimen collection devices. Together with its wholly owned subsidiaries DNA Genotek, Diversigen and Novosanis, it is a leader in the development, manufacturing and distribution of rapid diagnostic tests, sample collection and stabilization devices.
The company is known for creating and bringing to market the first over-the-counter infectious disease test, the OraQuick at-home oral HIV test, which has tested more than 76 million people for HIV since 2012.
In response to the COVID-19 pandemic, the company has leveraged its expertise in infectious disease testing and molecular sample collection with emergency-use authorizations for medical devices for rapid antigen self-testing and molecular sample collection for PCR-based tests.
The company’s portfolio of COVID-19 tests and collection kits feature easy, convenient and pain-free self-collection, and help increase access to testing while alleviating the burden on the health care system.
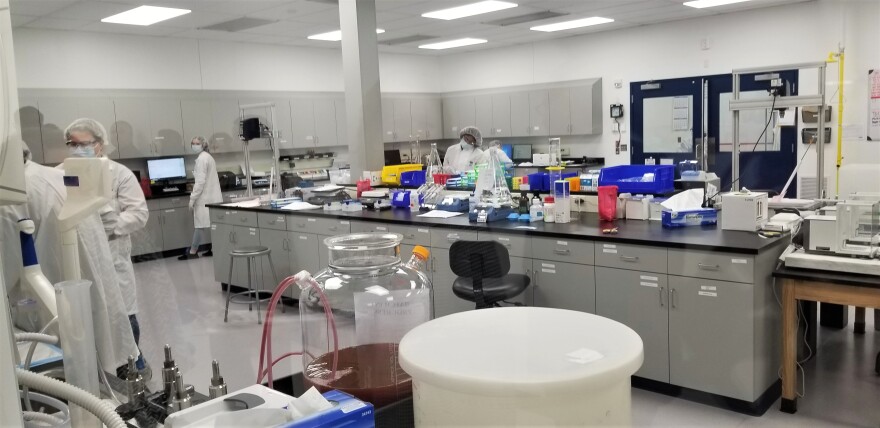
OraSure’s new facility would not have come to fruition if it weren’t for three contracts that were awarded to the company from the federal government last year: $205 million for the InteliSwab COVID-19 Rapid Test procurement, $109 million for InteliSwab manufacturing capacity build out, and $13.6 million to pursue full FDA 510(k) clearance for InteliSwab, said Lisa Nibauer, OraSure’s president of diagnostics.
Those contracts position OraSure as an “important part of the government’s global pandemic response,” Nibauer said.
“The baton was continually passed as the race to develop a test and get to market began."Lisa Nibauer, OraSure's president of diagnostics
Bringing the InteliSwab to the market was not easy, with hurdles at times seeming insurmountable, but OraSure teams “rose to the challenge and persevered,” she said.
“The baton was continually passed as the race to develop a test and get to market began," she said. "From [research and development] determining the right combination of antibodies for COVID-19 for use in our antigen test, to the clinical testing, to obtaining three FDA EUA’s, and then developing the marketing and selling plans to compete in an ever-changing landscape of new rapid tests, our teams rose to the challenge and I have never been more proud of the colleagues that I lead."
While OraSure had hundreds of millions of dollars of orders coming in because of the Delta and Omicron surges, the company was unable to fulfill all of them because it was trying to ramp up capacity at the same time.
It took a “Herculean effort” by workers to uncover numerous process improvements, which let the company increase output more than 500%, Nibauer said. Bit by bit, teams attacked inefficiencies, eliminated bottlenecks and overcame challenges, she said.
“As we shift our InteliSwab work to this brand-new facility, what we call our super factory, I know that we are positioned to succeed in the future as we implement automation and more efficient workflows,” Nibauer said.
Politicians applauded OraSure’s commitment to public health as well as its dedication to innovation, which continues to help the country battle the deadliest pandemic in its history.
Rep. Wild recounted numerous visits and phone calls with OraSure’s leadership throughout the pandemic and noted that she continues to be impressed by its “cutting-edge products.”
Sen. Casey called the ribbon-cutting a celebration of “excellence in health care technology.”
“The opportunity that [OraSure has] created to expand access to over-the-counter COVID tests has not only helped enhance our safety and helped us to open our schools and get people back to work, but it has literally saved lives,” Casey said.
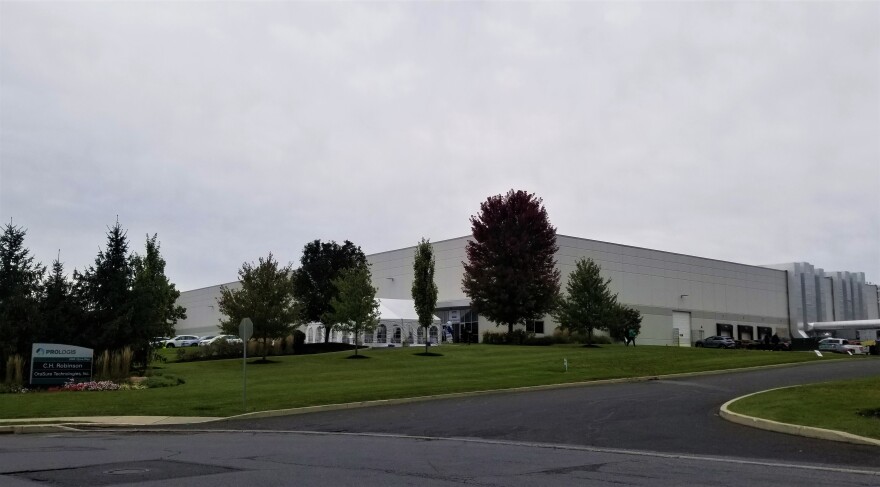
“The speed at which the scientists and employees moved to find a way to test for COVID was beyond remarkable,” state Sen. Lisa Boscola added. “OraSure has a legacy. It has been a legacy of working to solve difficult diagnostic challenges, and I’m proud that they call Bethlehem home.”
OraSure’s expansion means the creation and retention of more than 400 jobs in the Lehigh Valley region.
It also provides a boost to the “long legacy of manufacturing” in the Lehigh Valley, Wild said.
“Manufacturing is alive and well here in the Lehigh Valley, and I really couldn’t be prouder as a steelworker’s daughter,” Boscola said. “I know the importance of a manufacturing economy because it creates great, strong communities and also, it creates a working-class family, a middle-class family. They’re the backbone of our country, and it all starts with companies like OraSure.”
Following the ribbon-cutting, attendees were given a tour of OraSure’s new facility, which features more than 139,000 square feet of medical device manufacturing space.
The facility features warehouse space for bringing in raw materials, a staging area, formulation suites and production cells with automated assembly lines and machinery, according to Zach Wert, OraSure’s senior vice president of operations.
When the tour group asked why there was so much space, they were told the facility is designed to manufacture up to 110 million tests a year.
"So, you can imagine the amount of material you’d have to move in and out of the facility in an orderly fashion,” an official said.